We have entered a new Net-Zero Energy reality – one in which we can design and construct buildings that produce (on-site) all the energy they need – and we can do so within current project budgets and schedules. According to the New Buildings Institute, the last seven years have seen a 75 percent increase in the number of buildings verified as zero-energy and a 93 percent increase in the number of buildings tracking toward zero-energy – encouraging statistics that offer hope as we face the ever-increasing impacts of global climate change. Although complex, the process of creating high-performance buildings should not be perceived as overwhelming. It can be applied to a variety of building typologies and has definite synergies that align well with the characteristics and opportunities of school design. My work over the past decade on high-performance, zero-energy schools, most recently the NeoCity Academy in Osceola County, FL has provided several key lessons that are essential to achieving success on these project types.
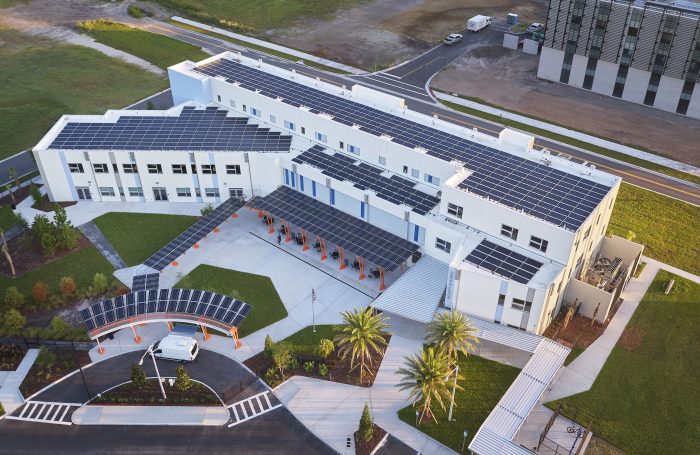
Lesson One. Doing nothing is a huge risk. Globally, the scientific community has reached a consensus on mankind’s contribution to the impact of climate change. Knowing this, our path to correcting these impacts should be clear: Eliminate waste; achieve the highest levels of efficiency; seek to heal the damage already done. Buildings account for 40 percent of the energy consumed in the US and 36 percent of the CO2 emissions. We spend $400 billion a year to power our homes, businesses, and schools, and 30 percent ($120B) of that is wasted via old, poorly detailed, inefficient buildings and systems, and failing infrastructure. Increasing costs and increasingly frequent and severe weather events have created the need to build better, more cost-effective, more resilient facilities. Without changing our processes for the design and construction of our built environment and how we live in those spaces we will only make that situation worse.
Lesson Two. Every project is unique. Everything from location (urban/suburban/rural) to micro and regional climate issues, to available infrastructure and jurisdictional politics, is different from one project to the next. Therefore, you must fully investigate these and other outside conditions and their influence on the project. These factors are the filters that will help determine project goals early in the process so the project team can live by them throughout the project. These goals are determined by the owner stakeholder group, are ranked in order of importance, and become the filter through which every decision is made throughout the design and construction process.
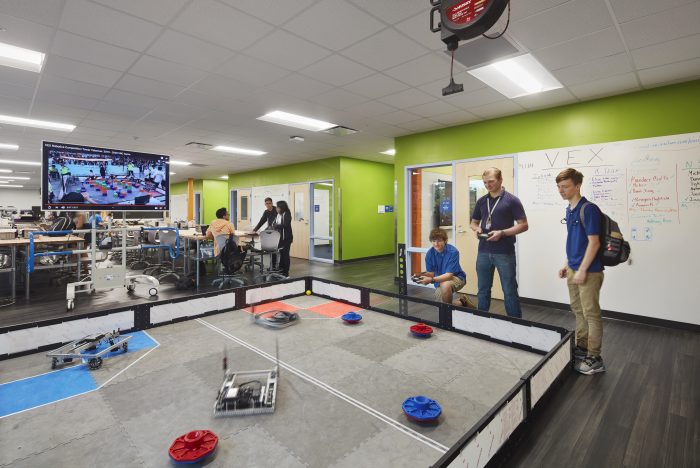
Lesson Three. Find a Champion. You need an internal team member to be the project’s sustainability champion. This person is the Rocky Balboa of the project and is most often someone on the owner’s team who has the authority to clear hurdles for the design and construction teams. High-performance design requires changes to the processes and challenges the mentality of “this is the way we have always done things.” A high-performance approach requires an open mind and a willingness to utilize data and experience to determine the best systems for the specific project. It is not a prescriptive process and one size does not fit all. An internal champion remains laser-focused on the end result, bringing together the project stakeholders with the design and construction teams to build consensus and ensuring project success.
Lesson Four. Leverage data analytics to aid decision-making. It is imperative that the design team create an energy model of the building early on and that it is continuously updated throughout the design and construction process. Due to finite resources on any project, the design team must look at costs, ROI and synergies with specific strategies that best support the project’s goals. For example, during the design of Discovery Elementary School, the design team evaluated a cost of $100,000 for triple-pane glazing. Using energy model scenarios, the team discovered we could reach the same energy savings with an increase in solar panel efficiency that cost only $9,000, allowing $91,000 to be shifted elsewhere in the project.
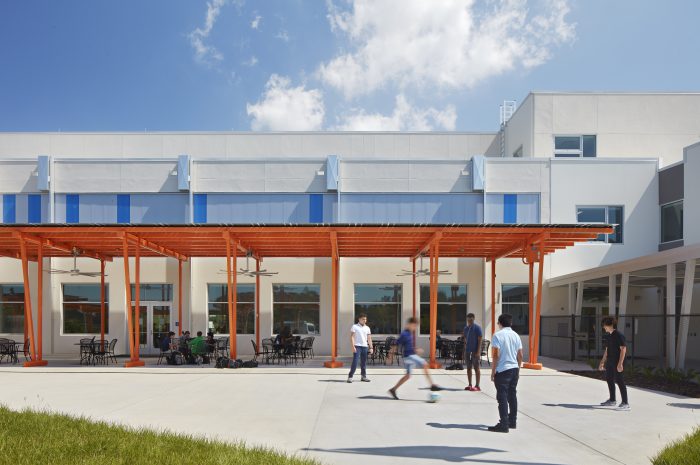
Lesson Five. There must be an Integrative approach to the design and construction process. High-performance buildings require specific sequencing and installation for the various components to work properly as a collective assembly. A finished LEGO® toy is complex but it is not complicated to build if you follow the steps. We take this approach in the construction process by implementing envelope commissioning that requires tested performance of the building to verify it meets the performance requirements set early in the design phase. The key to this process is to demystify the envelope details and utilize a third-party expert to verify the installation and implementation of the building envelope. This includes envelope coordination drawings, early on-site subcontractor coordination meetings, and constructing and testing envelope mockups prior to building installation.
Lesson Six. Create a high-performance building envelope. Up to 80 percent of “typical” energy loss can occur through a leaky building envelope. The key is to identify synergies in the materials that enclose the building. One of these materials is concrete. It is one of the strongest structural components you can use while creating a resilient, air-tight barrier for a building. Building joints, transitions between materials, and openings to the outside are all opportunities for conditioned air loss. An effective building envelope utilizes low-tech materials to create redundant layers of air and moisture sealing. Setting a stringent air leakage goal for the project will allow the HVAC systems to be right-sized, removing redundancy, and minimizing the energy footprint of the building.
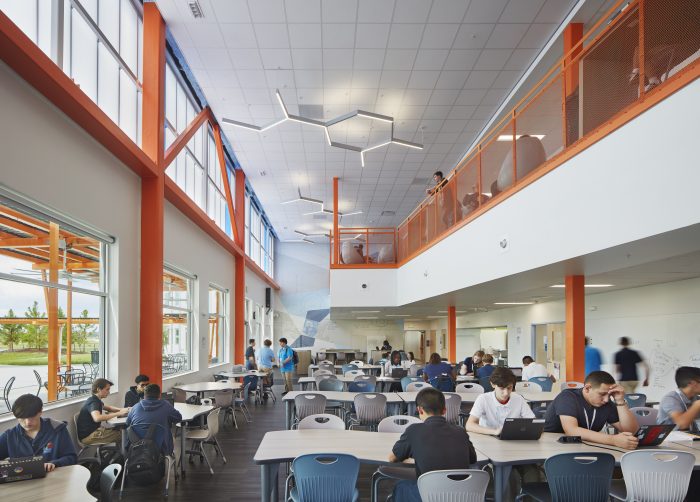
Lesson Seven. Trust but verify. The energy model, performance specifications, and execution of the construction all work in theory but the actual performance of the building systems must meet or exceed the design criteria in order to achieve the project goals. Close coordination with the contractor and sub-contractors is required to transform the design from theory to reality. The performance must be verified through the commissioning processes during and post-construction and maintained through the proper operation and maintenance of the systems moving forward.
High-performance, zero-energy buildings are quickly becoming the new reality and are accessible within today’s budgets and schedules. The demand is growing for projects like these as building owners are looking to reduce operating costs, increase health and wellness for building occupants, and increase resiliency within our communities. Successful high-performance design is a holistic process that can reduce a building’s energy use by up to 75 percent or more, which puts Net Zero within reach. It can then be achieved often using only the building’s roof area to host enough solar panels to offset a much smaller energy footprint of the building. Most importantly, high-performance buildings are resilient anchors in our communities that measurably improve the lives of the people who live, work, learn, and play in them.